Bulgaria: GaIN (Green IrrigatioN) - Green irrigation pipes for the future
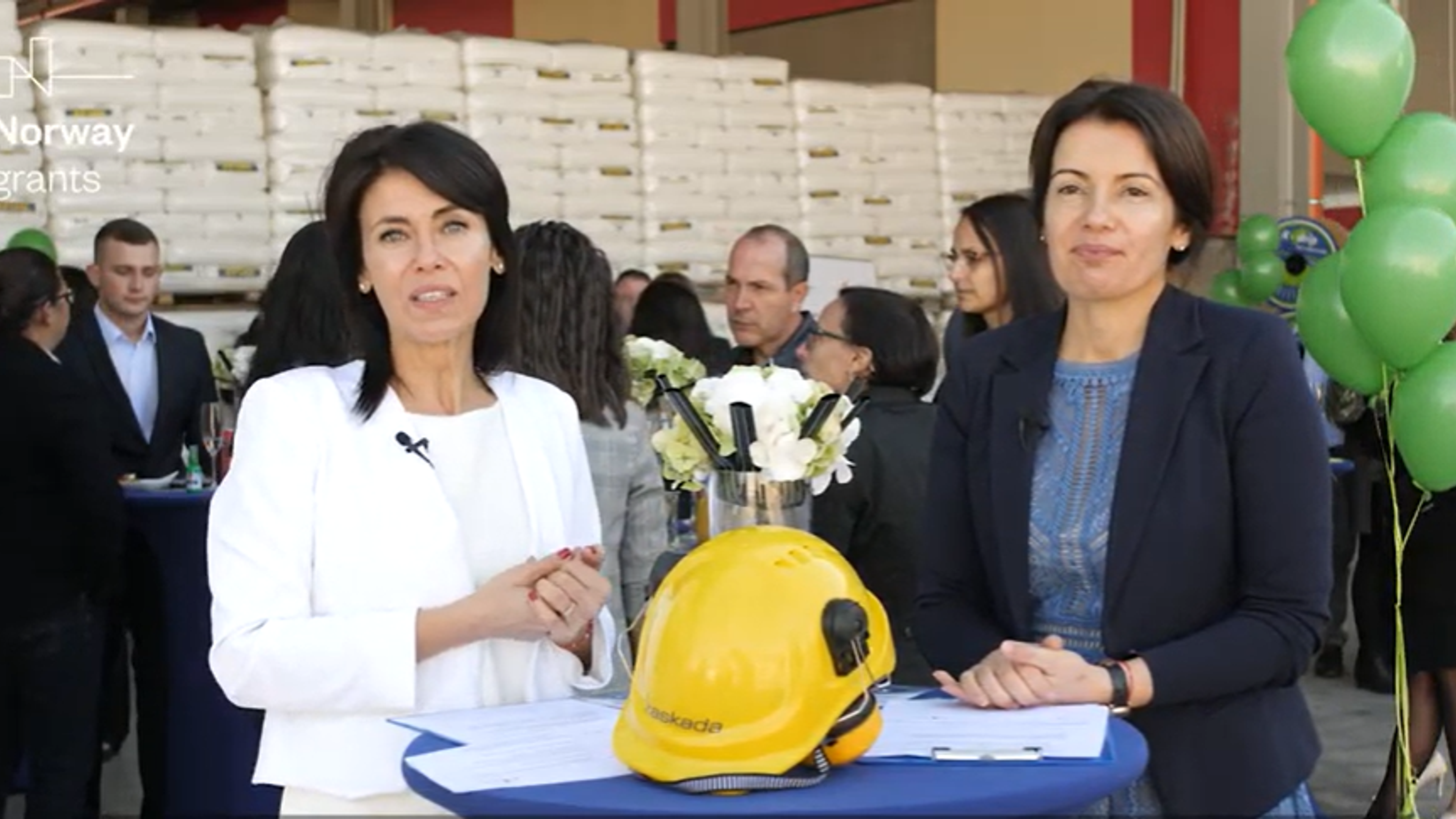
Kaskada is a family-owned Bulgarian company with 30 years of experience in recycling plastics close to the city of Plovdiv. This family business is developing in stages, without haste and without rest, but with a clear plan.
The company is managed by two sisters, Radostina and Ivanka. The sisters also run another activity in parallel – the transport of international cargo. The Norway Grants project perfectly combined these two activities. Via its logistics section, the company collect the drip irrigation pipes from the agricultural sector for recycling and follow-up in their new product.
Meet the Kaskada sisters:
Partnering up with International Development Norway AS
The Norwegian partner International Development Norway AS contributed with its expertise to analyse the situation in the new production facility and provide an action plan to transform it into a zero waste and emission factory.
A growing market
The production line is now fully operational and Kaskada has successfully entered the market for irrigation drip pipes in the agricultural sector. The global drip irrigation market is growing, as the drip systems are believed to be water-saving and important in mitigating the climate changes.
Plastic waste from the agricultural sector can be fertilisers, linings, sacks for seeds, feed bags, agrochemical containers, ropes, pipes and accessories for pipes. In 2017, 1243 million tonnes of plastic waste was generated from the agriculture farms in Europe. From this, less than half was recycled. With mechanical recycling, 0.262 million tonnes of the recovered was compounded (21.1% of the total) and energy used was 0.315 million tonnes (25.3%).
There is weak demand for recycled plastics and transforming the plastics value chain. While there are an increasing number of new processes for recycling polymers, the majority of the recyclable materials still end up in landfills or get incinerated, for logistical or geographical issues, lack of awareness and a lack of appropriate, readily available processing facilities.
An innovative approach
The project developed an innovative and environmental technological process for an irrigation drip tape with large application in agriculture sector.
The project applied an innovative in-house developed recipe in which 80% of prime grade high-density polyethylene (HDPE), which is the normally used for this type of production, is replaced by polymer compound consisting of recycled plastic materials. It will also start producing a tailor-made extrusion line for the production of the new product. The project has created jobs too.
The polymer is a ready compound, while when producing irrigation pipes the producers must mix different grades of polyethylene, additives and masterbatches. This gives huge benefits - easier production process and less expenses because the recycled material is cheaper and there are no additional expenses in production for additives and additional equipment.
The green production process will allow high levels of purification. Non-organic contaminations will be separated while in any other polymers there will be purification up to 99%. Even with the use of 80% of recycled product in the process of extrusion can still keep the high speed of the production line together with perfect quality of the pipes produced.
Want to learn more?
This is the longer version of the interview with the Kaskada sisters.
The Business Development, Innovation and SMEs Growth Programme in Bulgaria
The project is supported by Norway through the Norway Grants. See more opportunities under the SMEs Growth Programme in Bulgaria.
Follow the EEA and Norway Grants by Innovation Norway on Facebook or on LinkedIn to stay updated.